
It looks like your tool-change will be easiest to control with a G-code subroutine and configuring that as an A (or B or C) axis will make moving it from G-code easier. If it has a 4th servo then you might want to temporarily configure an A axis for the ATC carousel. How does yours work, and what does it need? There are so many options for ATC that I can't ever see the wizards being able to configure them all. In PNCCONF I don't get the option to configure the 5th stepgen used to drive the ATC. You might want to experiment with this simulated gantry configuration (without hardware) to see if it looks like it would work for you. There is a sample configuration in the standard installation which uses "gantrykins" which has some problems and irritations. It is supposedly easier with a development branch of LinuxCNC called joints_axes_4 which has a kinematic module called gentrivkins. There was some discussion about building it in to the standard homing code, but once you try to handle every single possibility (homing to switches, homing to encoder index, homing to encoder indexes that don't actually line up with each other.) it becomes quite a task.
AXYZ TOOLPATH FOR WINDOWS HOW TO
In theory LinuxCNC knows how to auto-square the gantry (though you would need independent limit switches). I'm not sure what the proper way to do this is. I need to be able to disable the drives to square the gantry and then re-enable. If the power-off behaviour isn't right then you might need a mechanical relay, crude though that sounds. I think that the 5i25/7i76 IO is high-impedence when unpowered so it will work properly (and safely). Is pin 8 something that I will connect to a gpio pin later on in HAL as a drive enable function? When the Direction line is at a low level the motor will rotate counter-clockwise and the SSt servo drive’s internal position register will increment for each pulse of the Step line.” With a standard motor cable the Direction line will have the following effect: With Direction at a high level, the motor will rotate clockwise (when viewing the shaft while facing the drive end of the motor) for each pulse of the Step line, and the internal position register (which is displayed by SSt-QuickSet's™ Status window) will decrement for each step pulse. Pins 18 and 9 go to the control board, pins 8,17,5 go to the power board. The OEM control only uses three pins (I think) to control the drives.
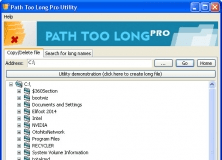
AXYZ TOOLPATH FOR WINDOWS SOFTWARE
The downside of this is the Toolpath software is awful, very time consuming and basic machining strategies. The OEM control work flow goes like this, DXF- proprietary software “Toolpath”- file transfer to machine RAM. The OEM control system works ok but is definitely the limiting factor as the hardware is quite good. Minimum downtime is essential as I use this machine for my business.
AXYZ TOOLPATH FOR WINDOWS PATCH
The way I’m doing the wiring is to patch into the OEM connectors so I can leave the existing control in place and functional until the Linuxcnc system is functional.
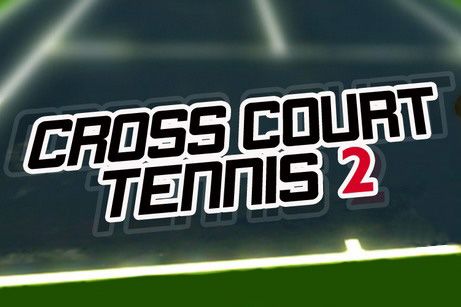
I’ve begun the process of retrofitting my router to Linuxcnc.
